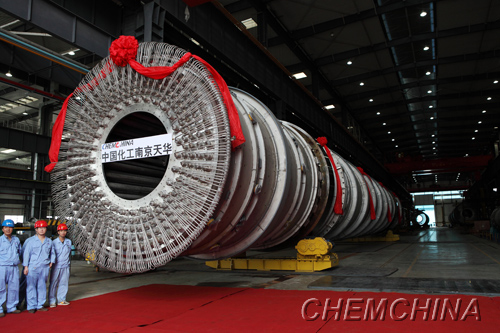
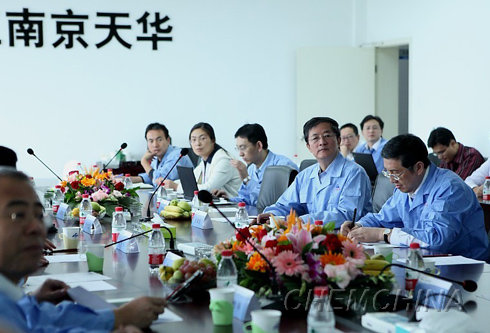
The world’s largest rotary steam tube dryer came off the production line, ready for delivery from Nanjing in East China’s Jiangsu province on Sep 20. It claims it has an annual production capacity of 4 million tons of purified terephthalic acid (PTA).
The machine was designed and developed by Tianhua Institute of Chemical Machinery and Automation, a subsidiary of the national leading chemical products company China National Chemical Corporation (ChemChina). The manufacture of the product filled a gap in the domestic market for dryers and brought the cost of purchasing it down by 50 percent. The drying unit consists of five different dryers: two with the diameter of 4.2 meters, two with the diameter of 4.5 m and one with the diameter of 4.8 m.
Drying consumes 20%-25% of energy in the whole process
The drying process is aimed at decreasing water use and other impurities contained in a certain material, to make it easier to be packaged, stored, transported and further processed. This procedure makes up 20 to 25 percent of the total energy consumption, so “developing advanced, efficient, energy-preserving drying equipment and process is extremely important to the industry”, said Xiao Shimeng, director of Tianhua Institute.
A decade ago, only a few developed countries made large-scale dryers of this kind, which were expensive and had shorter life spans. But the dryers manufactured by Tianhua in recent years featured higher processing capacities, efficiencies, safety standards and longer life spans. They have been welcomed not only in the domestic market, but also in many overseas countries including the United States, Spain and Belgium. “By using the home-developed large-scale drying equipment, we have greatly reduced the cost of industrial production, and thus indirectly reduced cost for consumers,” said Xiao. The large-scale dryers made by Tianhua had a generated output value of 1 billion yuan ($156.7 million) by the end of last month, and saved around $100 million in foreign exchange for the nation.
Advanced drying techniques promote energy saving in more sectors
Tianhua Institute plans to “further improve its PTA drying equipment, and transfer the technology to other fields such as the coal chemical, metallurgy, electricity and environment protection industries”, said Chen Hong, general manager of China National Chemical Equipment Corporation another subsidiary of ChemChina. “In the iron and steel industry, a dryer can save energy to the equivalent of 10,000 tons of standard coal a year,” Chen said.
Tianhua started to dry high-water coal in the power plant. This technology can bring coal consumption of inferior generators down by 5-15g/kWh, easing the resource crunch. At the same time, the reclaimed water can satisfy the needs of air-cooled and sea water-cooled generators, and supply water outside. Indonesia has applied the technology in a project that is running now.
As the only national research center of drying technologies and equipment in China, Tianhua Institute took part in 12 national research projects, was granted with more than 50 patents, and led the making of seven national standard products in the industry over the past decade.
Ren Jianxin, the general manager of its parent company, ChemChina, said the company “has been paying close attention to innovation and taking great effort in the commercialization of technologies”. “The world’s largest rotary steam tube dryer developed by Tianhua Institute is just one example of ChemChina’s innovative spirit,” he said.